News

Finding the Right Motor Controller, for the Right Application; in Space
For space missions, whether robotic or manned, to be successful, it is necessary for things to be able to move. On robotic missions, wheels need to be turned and arms extended. During manned missions, solar arrays need to be pointed and air circulation pumps need to operate continuously. Motor controllers are what enable the motors that provide these movements.
However, the environment outside Earth’s atmosphere means that engineers cannot buy a simple commercial off-the-shelf motor controller. The temperature and radiation environment in space and on other bodies in the Solar System play a significant role in the type of hardware that is space-rated. The need for reduced mass while minimizing mission risk due to component failure also places strict requirements on hardware.
Motor controllers are used for a variety of applications in space. Everything from the pointing of solar arrays to toggling valves in propulsion systems require fine motor control that is responsive and accurate. Without this sort of control, mission-critical systems would not perform as needed, jeopardizing mission success.
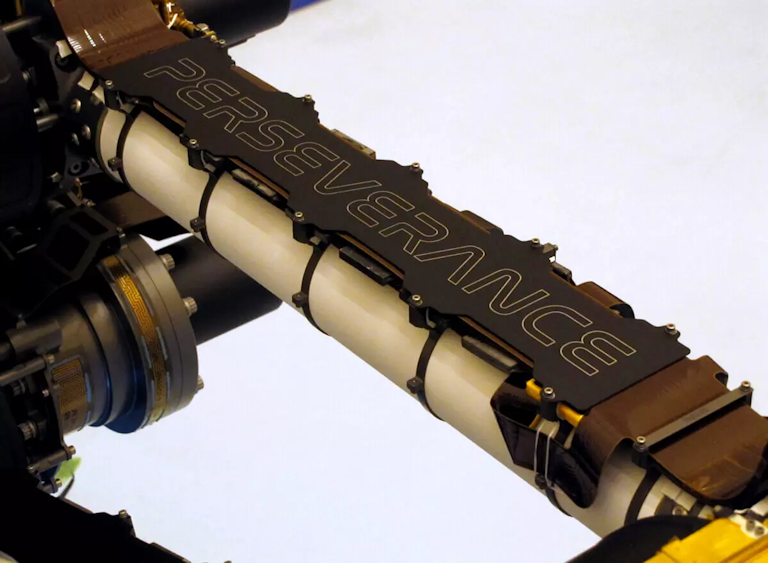
Motiv’s motor controllers are utilized on NASA’s Mars Perseverance Rover.
Motiv Space Systems has worked to develop a line of motor controllers that meet the stringent needs of a variety of space missions. With four controllers that can be customized to individual mission requirements, Motiv has demonstrated solutions for everything from gimbals to robotic systems. Each of the four controllers provides features and capabilities that are space-rated and ready for integration into the future of space exploration.
Alpha-II
Motiv’s Alpha-II motor controller has been developed to provide single-axis motion control for on-orbit robotic servicing and precision pointing. These capabilities have been demonstrated on missions such as NASA’s Restore-L and missions to Mars. The Alpha-II interface and proven operation make it the most versatile motor controller available for space-based applications.
Bravo
The Bravo motor controller provides two-channel control for stepper and brushless-DC motors. Whether the need is to enable precise positioning of mission-critical hardware or instrument mechanization, the versatility of the Bravo controller is unmatched among space-rated solutions. The simplified interface is ideal for robotics and gimbals, as well as optics and cryogenic cooling systems.
Delta
Motiv’s Delta motor controller is the smallest and most flexible control solution available. The mother-daughter board design of this controller gives operators flexibility in power output and I/O interfaces, making the Delta controller ideal for a wide range of applications. This single-axis motor controller can be used for instrument mechanization, robotics, gimblas, and nearly any other mission-critical motion system.
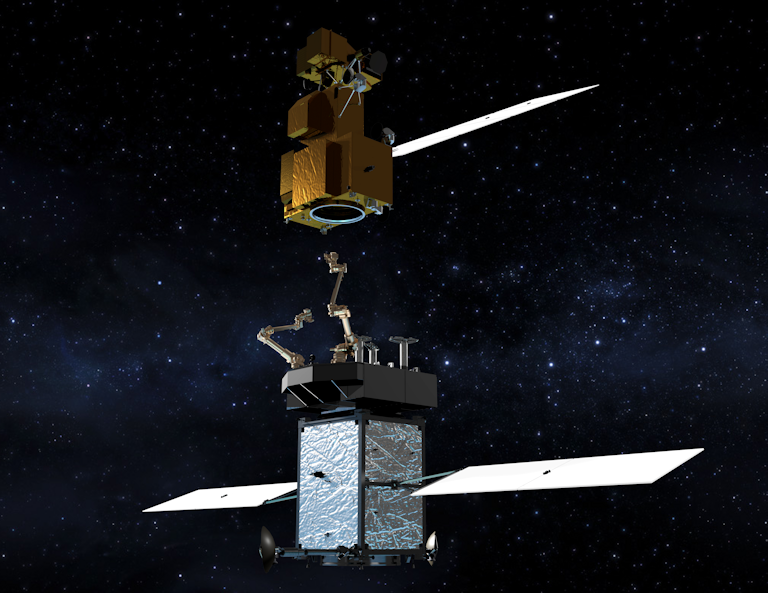
Artist’s rendering of the Restore-L mission using Motiv’s Alpha-II motor controller to capture and service a spacecraft. Credit: NASA
Echo
The Echo motor controller gives users a simple interface with only two wires to control brushless-DC motors. The small form-factor enables the controller to be packaged directly with the motor, providing the ability to replace existing brushed motor solutions. The Echo controller is well-suited for deployment mechanisms and pumping motors.
All of Motiv’s proven motor control systems provide space hardware operators with flexible solutions to meet specific mission needs. Moving things around is space is a challenge, but it is one that Motiv is committed to meeting to further exploration in Earth orbit, on the surface of the Moon and Mars, and beyond.